Made in the USA
Avoid the hassle factor and reduce cost of goods
USA VS. OFF-SHORING
With rising costs in other countries, DaMar Plastics has brought on customers since 2013 that have been reshoring products made in China. DaMar Plastics is competitive with off-shore manufacturers when all cost are considered, including development time, required trips to the source, shipping cost, duties, delays and loss of Intellectual Property protection. DaMar Plastics will work closely with you to reduce cost of goods through alternative materials, packaging, freight rates and plastic manufacturing processes.
Then there’s the “hassle factor”, distance and communication challenges that make doing business overseas more difficult.
“Made in USA” is gaining momentum with manufactures and consumers. Beyond cost and the sheer challenges of sourcing from other countries, there are growing issues with the amount of time products spend in the supply chain. Lead times have grown significantly so having the right product at the right time is becoming severely difficult. USA companies provide quality products that match or exceed products made in other countries.
13 Reasons Why Producing Your Product in the United States is better than going Off-Shore.
- Reduces lead-times. No long lead-time to get purchase order acceptance, materials procurement, production scheduled, parts made and shipments completed.
- Reduces inventories. Upside volume in sales can be quickly accommodated.
- Reduces shipping time. If your product is coming from overseas (such as Asia), it could take 30 – 90 days OTW (on the water) for shipments to arrive and get through the ports and customers. U.S. shipments only take 1-5 days.
- NO delays due to U.S. Customs or Ports of Entry inspections.
- Shipping rates are reduced when products are sourced in the U.S. Shipping containers costs have exploded then once products clear customs there is still inland freight charges.
- There are no duties on goods produced in the U.S. There are no assist papers that need to be filed.
- Reduced development time. Normal time for a product from concept through tooling to first article in the U.S. is about 8-12 weeks. If produced in Asia, the time is about 6 months and several trips.
- Reduced time and cost to visit your supplier. Costs to send an engineer or procurement person to an off-shore company can cost thousands of dollars, and a week out of the office, where U.S. based factories cost significantly less to get to and can be done overnight.
- Intellectual property is much safer in the U.S. Asia has a history of counterfeit goods being produced and shipped to the states creating competition for your own product. There are no laws being enforced in Asia to protect U.S. companies from being “knocked-off”. Trademarks and Patents are largely ignored in Asia and other foreign countries.
- Communications are very difficult when doing business off-shore and can cause costly mistakes. Language differences are often the reason.
- Time zones hinder development and production schedules. With up to 14 hour time differences, delays of at least one day to get responses to questions and issues are not uncommon.
- Quality issues are easily managed in the U.S. Quality issues from off-shore may require on-going back and forth several times causing huge delays. If new production is required, another production cycle, including time on the water is required.
- Less control. Many of the consumer products produced off-shore for the U.S. find their way to the “street market” and diminish the good name of the manufacturer and increase cost.
Summary
DaMar Plastics injection and blow molding services can be competitive with off-shore when all cost are considered, including development time, required trips to the source, shipping cost, duties, delays and loss of Intellectual Property protection.We go above and beyond to make sure our customers get exactly what they need when they need it at an affordable cost, which is how we got our ISO 9001 Certification!
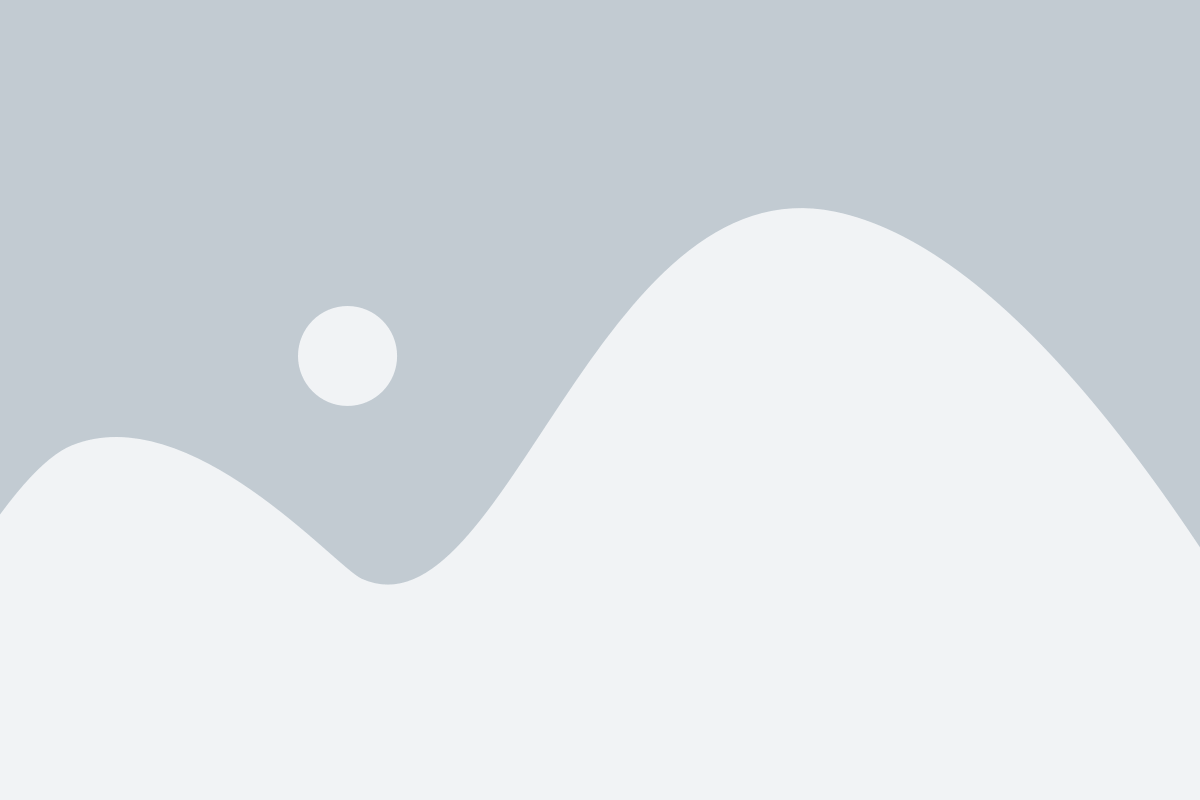
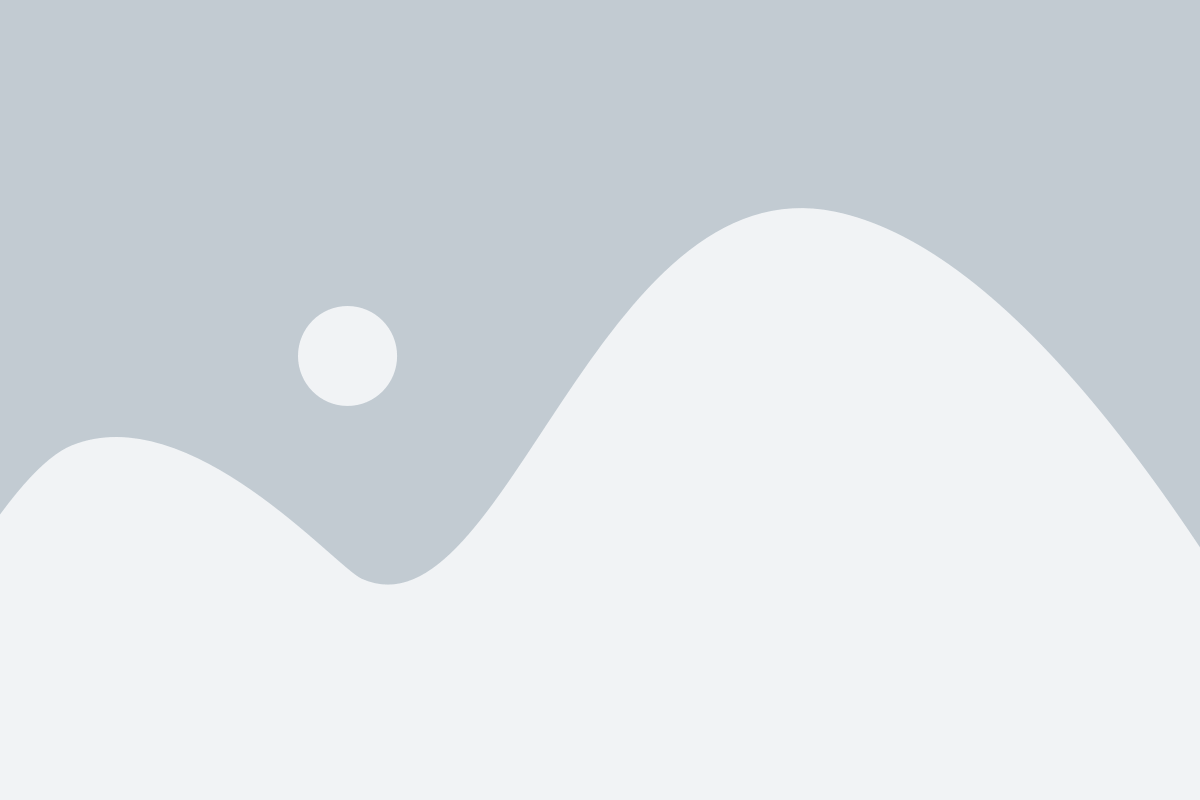
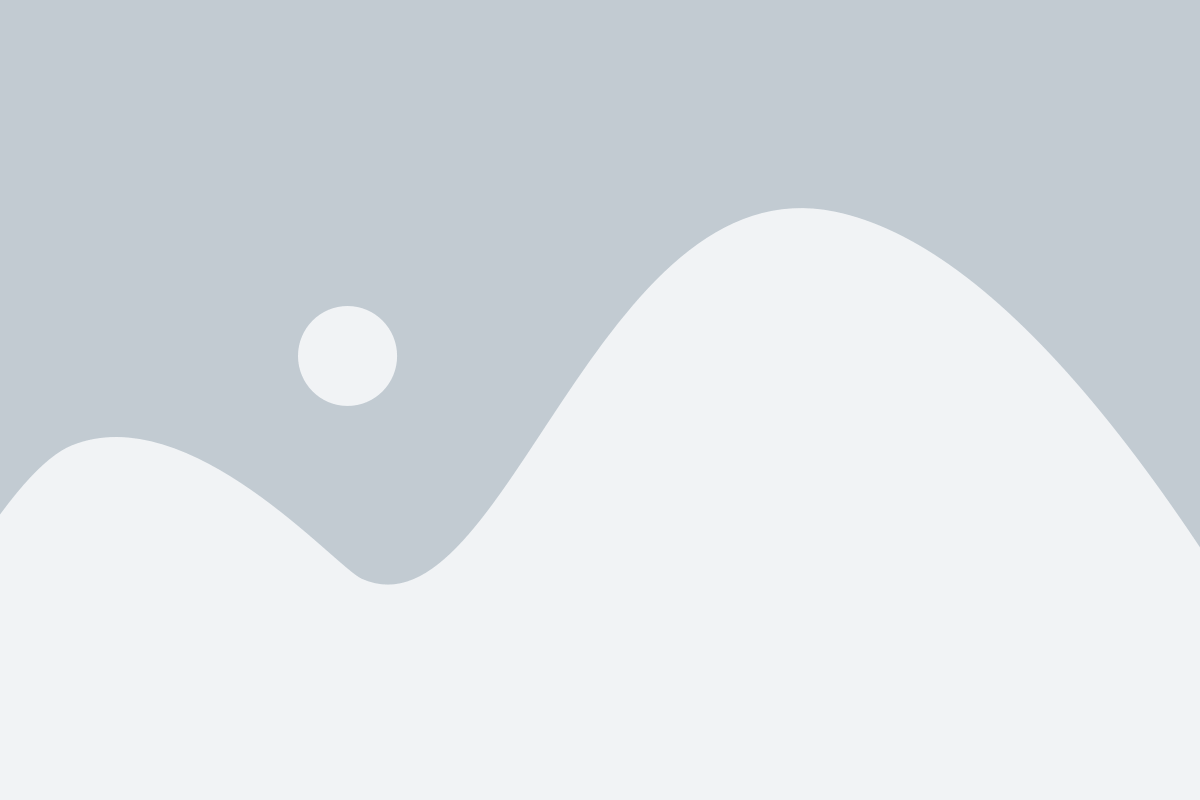